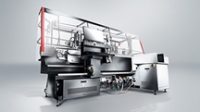
Harness Manufacturing/Máy gia công dây cáp điện Zeta 640/650
Highly flexible automation/Chế độ gia công tự động độ linh động cao
- Production time reduced by up to 50%/Giảm thời gian thao tác xuống 50%
- Continuous data flow from ECAD or DLW to the machine/ Dữ liệu được chuyển liên tục ECAD hoặc DLW đến máy
- Economic just-in-time-production from a batch of 1 and up/ Chế độ sản xuất đúng thời điểm tiết kiệm từ lô hàng số 1 và các lô tiếp theo
- Wire deposit in the correct order for the follow-up process/ hệ thống luân chuyển dây theo các trình từ chuẩn xác cho các quá trình tiếp theo
Maximum productivity without changeovers/Đối ưu hóa năng xuất mà không cần phải chuyển đổi nhiều máy
- Up to 13 process modules/ có đến 13 modules gia công trên máy
- Automatic wire selector with up to 36 different wires/ Hệ thống tự lựa chọn dây cáp điện lên đến 36 loại
- Automated marking with inkjet/ Máy in phun đánh dấu tự động
- Large cross-section range: 0.22 – 6 mm²/Kích thước dây đa dạng: từ 0.22 đến 6mm2
Reliable processing with high quality/Nâng cao chất lượng gia công
- Fully automatic production guarantees continuously high quality/ Hệ thống sản xuất tự động hoàn toàn đảm bảo chất lượng gia công cao liên tục
- Optional quality test modules/Quý khách có thẻ chọn thêm option Moldules kiểm tra chất lượng
- Các mẫu máy nâng cao của máy giá công dây cáp điện Zeta 640/650 như: Zeta 630, Zeta 740/750; Zeta 745/765
The industry places the highest demands on the flexibility of automated wire assembly, requiring that it be possible to process many different cables and terminals without changeovers, just-in-time, for batches of any size. Komax developed the highly flexible Zeta 640 and Zeta 650 for this reason. They allow automated processes and batch or sequential production without the need for changeovers, cutting the manufacturing time by up to 50 percent. EtherCAT improves the overall system performance and significantly increases output. With continuous data flow, the new Zeta machines are ready for their efficient future.
Greater flexibility for batches and sequences
The fully automatic wire processing machines of the latest generation provide maximum flexibility for specific manufacturing across a wide range of applications. The Zeta 640 is equipped with five process modules in the standard configuration, opening up many new possibilities for small batches or sequences. The Zeta 650 is designed for eight modules, which reduces changeovers and interruptions to a minimum. Both machines can be extended by five additional modules along the transfer section as necessary.
Time savings of up to 50 percent
The new generation Zeta reduces manual processes to a minimum. It automates all processes such as cutting to length, stripping, labeling, sleeve insertion, etc., as needed and simultaneously on both wire ends. Three pairs of blades cover the entire cross-section range, enabling production without the need for changeovers. The high-quality, durable components permit high process speeds, which in turn shortens lead times.
Wide variety with up to 36 wire types
Versatile control cabinet construction requires many different materials such as wire types, terminals or ferrules. These are available on the Zeta 640/650 without the need for changeovers. The automatic wire changer provides up to 36 different wires from the entire cross-section range. Up to two automated inkjet printers mark the wires in black and one additional color within the same sequence.
Correct order for further processing
The new Zeta machines process the required wires from A to Z in a single process step. Tied up as needed and sorted in the correct order, the bundler wire deposit provides the wires separately for further processing according to sequence or batches. This simplifies and significantly accelerates installation in the control cabinet and logistics. The wires can be removed mid-production. The binding method is freely defined for each wire, independent of the mode – batch or sequence production.
Continuous data flow to the machine
Data export from any system (ERP, ECAD, DLW, Excel cutting list, etc.) can be easily converted into readable data (TopConvert). This production data is then sent directly to the machine via the WPCS Komax interface. Manual programming of items in the machine is eliminated, making entry error-free and highly efficient – even with a batch size of one.
Continuous high quality thanks to automation
The continuous data transfer minimizes errors as manual entry on the machine is not necessary. The fully automatic production guarantees reproducible, continuous quality. Crimp height and pull-out force measurement is integrated and defective wires are automatically separated. Further quality monitoring like the automatic conductor detector (ACD), are available as an option.
Versatile configurations and options
An extensive range of process modules and options enables flexible configuration of the Zeta 640/650. The large number of terminal parts in the industrial sector can be processed with the C1370 crimp module. The CM 1/5 GS ferrule module is able to accommodate five taped AEH rolls simultaneously. A double gripper module enables the production of horizontal and vertical double crimps. Modules for untwisting and separating batches complete the processing possibilities.